What is Fiber Optic Sensing?
Distributed Temperature Sensing (DTS), Distributed Temperature and Strain Sensing (DTSS) and Distributed Acoustic Sensing (DAS) are all various types of fiber optic sensing technologies which use the physical properties of light as it travels along a fiber to detect changes in temperature, strain, vibration (acoustics) and other parameters. Fiber optic sensing utilizes the fiber as the sensor to create thousands of continuous sensing points along the fiber. This is called distributed fiber optic sensing where the fiber itself acts as a distributed fiber optic sensor.
Fiber optic sensing uses the physical properties of light as it travels along a fiber to detect changes in temperature, strain, vibration (acoustics) and other parameters. Fiber optic sensing utilizes the fiber as the sensor to create thousands of continuous sensing points along the fiber. This is called distributed fiber optic sensing where the fiber itself acts as a distributed fiber optic sensor.
The devices measuring the fiber itself are generally called interrogators. The purpose is to use a standard or specific fiber for measuring the temperature, strain or vibration along it using Raman, Brillouin or Coherent Rayleigh backscattering Distributed Fiber Optic Sensing techniques.
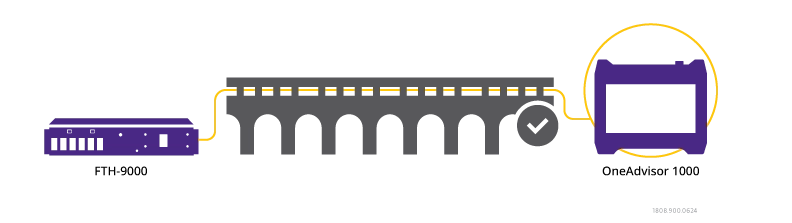
For instance, by using fiber sensing interrogator, one can:
- Detect and locate any hot spot along a power cable.
- Detect and locate any excessive strain on an optical telecom cable and react before it breaks.
- Detect third party interference on pipelines or data center interconnects (DCI)
Below are examples of fiber sensing applications:
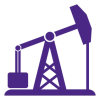
- Fatigue monitoring
- Leaks and flow lines blockage
- Reservoir monitoring
- Thermal oil recovery
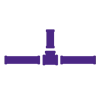
- Leak detection
- Ground movement monitoring
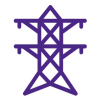
- Hot spot detection and localization
- Ampacity (Real Time Thermal rating...)
- Smart Grid
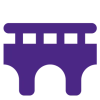
- Crack detection
- Infrastructure management and design
- Dam, dike
- Seismic areas
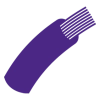
- Buried fiber optic cables monitoring
- Aerial cable monitoring
- Overstressed fiber identification
- Fiber aging
A fiber optic cable can act as the communication path between a test station and an external sensor, which is known as extrinsic sensing. However, when the fiber itself acts as the fiber optic sensing system, this is known as intrinsic fiber sensing.
The benefit of this type of fiber sensing technology is that discrete interfaces between the fiber and external sensors are not required, which reduces complexity and cost. In order to make this possible, external stimulation such as temperature, strain or vibrations (acoustic waves) need to influence the light guided within the cable in a measurable way to provide useful data.
When light photons are scattered randomly by the fiber material, this is known as Rayleigh scattering. This principle has proven useful with various types of fiber testing techniques such as OTDR fiber testing because the intensity, wavelength, and location of light backscattered to the detector can determine the magnitude and position of attenuation and reflection events within an optical fiber.
In a similar way, Raman scattering produces temperature-induced changes in photons scattered back to the source in the Stokes band. By measuring the difference between the intensity of backscattered light in the Stokes and anti-Stokes bands, the temperature can be accurately determined at any given location along the fiber.
Brillouin scattering is a similar phenomenon where the backscattered light wavelength is influenced by the external temperature and acoustic stimulation in a predictable way. This data, when coupled with background knowledge of temperature at the same point, can be used to accurately determine the strain experienced by the fiber and analyzed to determine what areas (zones) of the fiber are impacted.
Rayleigh coherent scattering can be used to detect vibrations and acoustic waves. The phase shift of the light is sensitive to vibrations and acoustic waves that the fiber optic cable experiences. By analyzing these phase shifts the location and intensity of the vibrations along the entire length of the fiber can be pinpointed.
Distributed fiber optic sensing
Raman, Brillouin and Rayleigh scattering are effectively used in Distributed Fiber Sensing (DFS). Raman scattering is used for Distributed Temperature Sensing (DTS), Brillouin scattering is used for Distributed Temperature and Strain Sensing (DTSS), and Rayleigh scattering is used for Distributed Acoustic Sensing (DAS). These measurements can be used to monitor the temperature, strain and vibrations accurately over tens of kilometers.
In this context, "distributed" simply refers to fiber sensing technology that can measure continuously throughout the complete length of the fiber, or distributed fiber optic sensor. Essentially, the fiber itself is the sensor. Since these fiber sensing methods are completely intrinsic, standard telecommunications fiber can be used as the medium, if the temperature is expected to remain below 100˚C (212˚F), and the fiber is not subjected to excessive chemical or mechanical disruption.
How fiber sensing evolved
Before fiber optics had emerged on the scene as a telecommunications method in the 1970's, the obvious potential of fiber for sensing applications was already being realized. The fotonic sensor, an extrinsic fiber sensor used for non-contact vibration measurements, was patented in 1967. By the mid-1980's fiber optic gyroscope principles had been established. By tracking the phase shift of the laser light source contained within the fiber, precise rotational data could be obtained.

The same components and infrastructure developed for communication fiber optics, including single-mode fiber and couplers and splitters, were equally suitable for fiber optic sensing infrastructure. Immunity to electrical stimuli, long distance range, and resistance to corrosion were additional attributes that were advantageous for fiber sensing. Although the first intrinsic fiber sensing was developed in the 1970's, it wasn't until the early 1990's that distributed fiber optic sensing gained widespread use for temperature, strain, pressure, acoustics, and other measurements. The oil and gas industry was one of the first industries to realize the tremendous benefits of a fiber optic distributed temperature sensing system in the late 1990's.
During this same period, fiber Bragg grating was being developed using a modified fiber construction with microscopic optical "mirrors" patterned into the full length of the fiber. Although this discovery was made accidentally during a series of argon-ion light experiments, it has proven useful for some types of optical fiber sensing.
The gratings act as a filter, reflecting selected wavelengths and allowing others to pass. The wavelength reflected can also vary depending on temperature, strain or pressure, so that a specific signature will be created at each grating in the fiber. Although this format has been effectively used in many industries, it requires specialized fiber construction and very high-resolution wavelength analysis, making it cost prohibitive for some distributed fiber optic sensing applications.
In 2017, the non-profit Fiber Optic Sensing Association (FOSA) was established to educate the public, government and industry insiders on the benefits of fiber sensing. Based on the vast array of current and potential benefits, FOSA produces educational content espousing the use of fiber optic sensing to influence subjects as diverse and far-reaching as seismic activity, human-trafficking, and transportation. The association and its leadership have given a voice to ground-breaking fiber sensing technology.
Here are a few applications which can be addressed with fiber sensing interrogators.
- Optical Network Sensing: protect, inspect, or monitor optical fiber networks
- Infrastructure Monitoring Sensing: a fiber can be used to conduct infrastructure monitoring by using the fiber as a probing device. In this use case, one can deploy a fiber along critical infrastructure such as a bridge, pipeline, secure access point/opening or dam wall to set off an alarm if the fiber demonstrates sudden strain, movement, or the temperature of the fiber puts the infrastructure at risk of damage or failure. This can be used to secure openings such as doors or manhole covers to generate an alarm if the opening is breached.
- Infrastructure Protection: acoustic sensing can be used to identify and localize threats (intentional and non-intentional) around critical assets such as borders, railways, electrical cables and pipelines to protect infrastructure.
Several infrastructure monitoring applications are available with VIAVI fiber sensing interrogators.
- Detection of ground movement and third party interference along a pipeline
- Detection of mechanical deformation of the pipeline
- Detection and location of any leakage along a pipeline, dike, dam etc.
- Detection and location of any threat or stress point in a telecom optical network
- Detection and location of any thermal hot spot or proximity warnings along a power cable
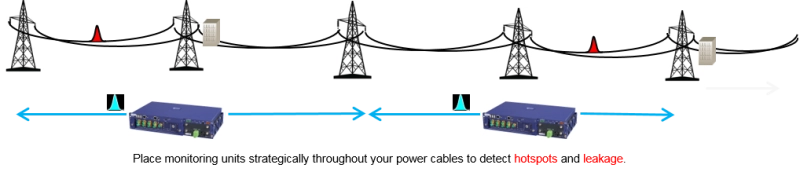
Using a portable instrument, such as the OneAdvisor platform with a DTS or DTSS capability, an inspector can go out into the field and conduct field measurements on fibers. Alternatively, using ONMSi and a rack-mounted Fiber Test Head with DTS, DTSS or DAS capability, fibers can be monitored long term and alarms raised if there are changes or events detected.
Below is an example of the VIAVI DTSS:
- VIAVI DTSS interrogator is Brillouin OTDR (BOTDR). A short pulse of light is launched into the fiber used as a fiber optic sensor. The forward propagating light generates Brillouin backscattered light at two distinct wavelengths, from all points along the fiber.
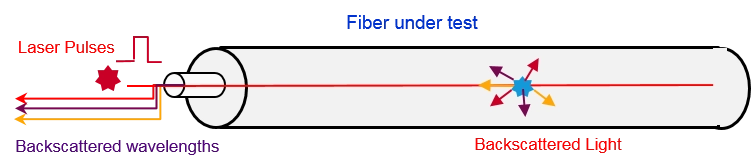
- The wavelengths of the Brillouin backscattered light are different to that of the forward incident light and are named "Stokes" and "anti-Stokes". The difference of Stokes and Anti-stokes Brillouin level and frequency is an image of temperature and strain along the fiber.
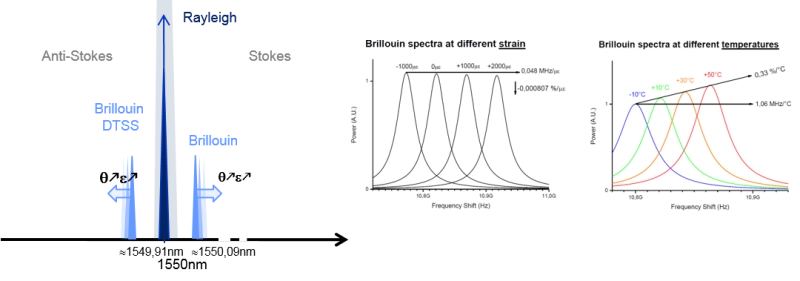
How can fiber testing shorten repair (MTTR) of critical infrastructure or a fiber network?
Fiber monitoring provides an immediate alarm when a change is detected. It can also provide a geo-located map pinpoint for the location of the event detected on the fiber. This allows the organization to dispatch to inspect the fiber or to fix to the right location every time and eliminate the longer period of time that would be required for finding a problem along a fiber. Learn more about fiber testing.
Customers of telecoms service providers and data centers leasing dark fiber will report a service outage caused by a fiber break but often when there is a break, the cable has been strained permanently on either side of the break or damage event. Take the example of a backhoe digging up a cable. The cable was pulled, tugged and strained. Strain inspection will allow a technician to determine exactly which section of the cables need replacement and allow the cable owner to hold the party responsible for the damage accountable with DTSS fiber optic sensing evidence. The same is true for damage caused by inclement weather and debris such as tree branches falling on aerial cables.
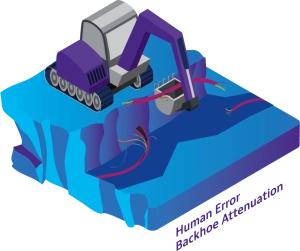
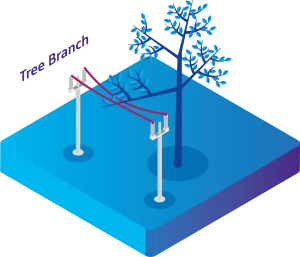
The most common but difficult to diagnose issue in the fiber of a network occurs when excessive strain is placed on the fiber. This permanently elongates the fiber, weakening it and potentially changing its light transmission properties. Below is an image of a strain test that shows three strain peaks using DTSS. All three areas of this fiber are compromised but a classic Rayleigh OTDR will not reveal this problem. These peaks indicate this fiber needs replacement.
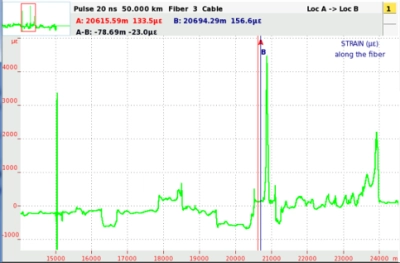
Fiber sensing technology offers a powerful solution for power utilities to enhance the monitoring and maintenance of their infrastructure. By utilizing optical fibers integrated within power cables, utilities can achieve real-time, continuous monitoring of key parameters, enabling proactive measures to prevent damage and avoid costly repairs.
Power lines are exposed to various environmental and operational stresses that can lead to overheating, mechanical strain, and potential failures. Fibers installed along the power lines can be used to monitor temperature, strain, and vibration in real-time. For instance, detecting hotspots can indicate areas where insulation may be degrading or where there is an overload condition. By identifying these issues early, utilities can schedule targeted maintenance before a minor problem escalates into a major failure, thus preventing power outages and reducing repair costs.
Another significant advantage of fiber optic sensing is its ability to precisely locate faults along power lines. Traditional fault detection methods can be slow and costly, often requiring extensive manual inspection using trucks, helicopters, or drones. Fiber optic sensing can quickly identify and locate faults caused by physical damage, environmental factors, or operational anomalies. This rapid fault location capability enables utility companies to respond swiftly, minimizing downtime and ensuring a more reliable power supply
Given the wide range of benefits already realized through fiber optic sensing in multiple industries, it is safe to assume the efficacy and cost-effectiveness of existing products will continue to improve just as new applications are developed. FOSA has explored many of these possibilities in depth, including the use of fiber sensing in "smart cities", integration of the Internet of Things (IoT), and innovative new fiber variations designed specifically for more challenging environments.
Fiber optic shape sensing is a new process that enables real-time, accurate positioning data over long spans and complex geometries. With the fiber either embedded within or attached to the object of interest, structures like wind turbines, tunnels, and high-rise buildings can have their form factor continually monitored and tracked simultaneously with temperature, pressure and other parameters.
This same shape sensing capability can even be used to explore and diagnose the human body in new medical device innovations. Fiber optic sensing can be used to track surgical instruments, support imaging, and even diagnose vascular conditions. With border security becoming increasingly relevant, further use of fiber optic sensing technology might also lead to more deployment of fiber optic "fences" that can pinpoint intrusions without the cumbersome physical barriers.
Although the phenomenal data transfer and communication breakthroughs made possible through fiber optics are widely recognized, the vast array of distributed fiber sensing capabilities supported by these same basic components are perhaps less well known. As society becomes more connected, the demands for monitoring, security, and minimized reaction times will continue to grow. Creative utilization of fiber optic sensing will help make this possible.
What type of fiber optic sensing interrogators does VIAVI offer?
The VIAVI fiber sensing portfolio includes:
- DTS (Distributed Temperature Sensing) based on Raman OTDR technology
- DTSS (Distributed Temperature and Strain Sensing) based on Brillouin OTDR technology
- DAS (Distributed Acoustic Sensing) based on coherent Rayleigh backscattering technology
Get started with VIAVI today!
Are you ready to take the next step with one of our fiber sensing products or solutions?
Complete one of the following forms to get going: